Carbon fiber sheets vs steel and aluminum sheets
by 03/03/2021 19:030
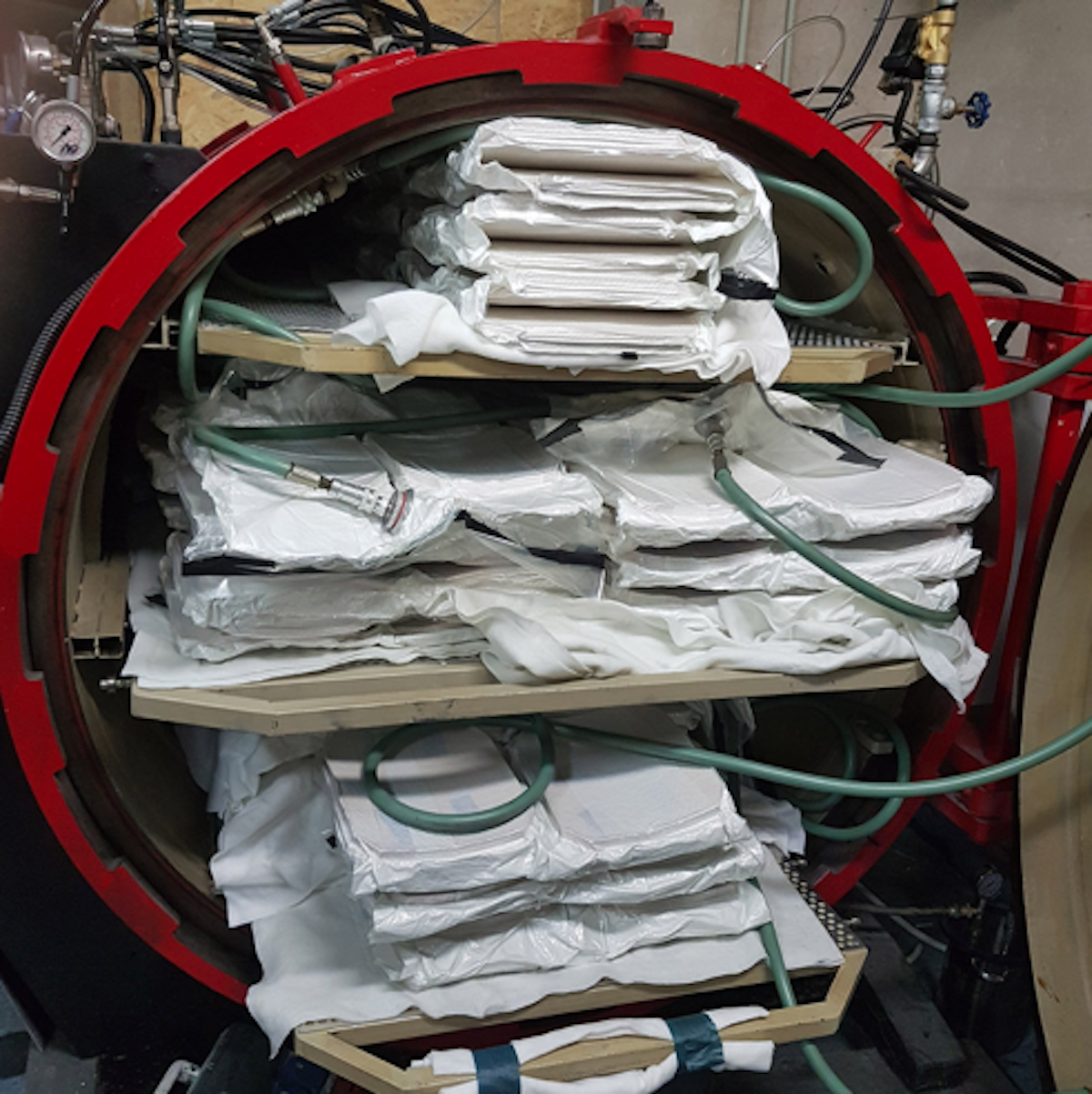
Body : A never-ending, long debate seems to initiate when it comes to the selection of material for sheets–whether carbon fiber ones are superior or steel and aluminum give an edge. Everyone appears to be giving their own opinion, puzzling the consumers even more. However, in this article, we will be sharing a depth and holistic comparison of carbon fiber sheets versus steel and aluminum ones. All these materials posses’ pros and cons, making them suitable depending on the intended use and the purpose of the users.
This last decade has seen an increase in the use of carbon fiber sheets and composites as opposed to these traditional metals. But before we begin, you need to have some basic understanding of carbon fiber and how it is manufactured. Although carbon fiber can be produced through various methods one of the most common ones (also the one used to manufacture Formula one cars) is the prepreg autoclave composite method. Carbon fiber manufacturing begins with carbonization. Precursor polymer with a high percentage of carbon atoms is drawn into long fibers and then heated in an anaerobic environment. In this process of carbon fiber molding, these molds are most commonly made from carbon fiber. Afterward, prepregs, most widely carbon fibers, are impregnated with resins and used to form prepreg composites. Now, these composites are placed in an autoclave, a system that simultaneously produces high pressure (up to 8 bar) and high temperature (120-150°C) to make sure layers of composites are compressed tightly and eliminate any air bubbles.
We will be listing specific properties common to all these metals and differentiate between them to check which of these metals performs better.
Density/ Weight and Rigidness
The increased usage of carbon fiber panels as opposed to steel and aluminum in recent years can be attributed to its low density yet providing rigidness at the same time, making it extremely suitable where maximum strength is to be obtained while keeping the weight minimum. Carbon fiber composites have a density of 1.55 g/cm3, while in the case of aluminum, it is 2.7g/cm3 and 7.9 g/cm3 for steel. This makes carbon fiber composites almost x 2 lighter than aluminum and x 5 lighter than steel. A material’s stiffness is measured using Young Modulus, and according to experiments, a block of carbon fiber offers a stiffness of 90.5 GPa, whereas this figure stands at 69 GPa in the case of aluminum. If we compare similar weights, carbon fiber is also two to five times stiffer than steel and aluminum sheets. All in all, carbon fiber sheets provide an ideal weight to stiffness ratio among all the materials, making them suitable for F1 cars, unmanned aerial vehicles (UAVs), and aviation parts that need to be lightweight to enhance efficiency.
Furthermore, due to its low density, carbon fiber can conveniently be machined by using CNC machines other tools such as an angular grinder.
Manufacturing Cost
However, the use of carbon fiber sheets comes at an expense, and the most significant factor is the high cost of carbon fiber manufacturing. A highly specialized production facility is required, not to mention the expensive raw material: carbon fiber fabrics. Besides, the manufacturing of carbon fiber composites requires carbon prepreg composites to be manually placed in the molds, making it time-consuming and costly at the same time. Also, due to the distinctive nature of carbon fiber products, the production requires specific placement of fabrics, making the process expensive. Carbon fiber, one of the raw materials used for production, is expensive and cost as much as EUR 50 per m2 (carbon fiber prepregs). Also, it is very costly to use it for manufacturing, e.g., autoclave, which is invaluable for producing high-quality carbon fiber costs in between EUR 200-400 thou. All these factors account for the limited use of carbon fiber on a large scale.
Thermal Expansion
All of these materials show various characteristics of heat expansion. Heat expansion refers to the change in material dimensions due to a temperature change. Carbon fiber panel displays almost zero heat expansion, thus making it extremely important in devices such as 3D scanners, telescopes, and other devices where minimum heat expansion is the key. In contrast to carbon fiber, steel and aluminum fiber perform poorly on this index, with steel having thermal expansion three times greater and aluminum having six times than carbon fiber.
Thermal resistivity
Talking about thermal resistivity, carbon fiber panels seem to lag behind the steel and aluminum sheets as they are not able to absorb higher temperatures, making them unsuitable for use where high temperature needs to be maintained. Standard carbon fiber composites can only withstand temperatures up to 70 to 80 degrees Celsius. Even the most rigid ones have the property only to resist a maximum of 100 to 160 degrees Celsius. However, this comes as an additional cost of carbon fiber prepreg. Comparing to the thermal resistivity of steel and aluminum, these numbers seem trivial. Steel can resist temperatures as high as 870 C, whereas aluminum till 650 degrees Celsius.
Impact Resistivity
Although carbon fiber provides an edge over steel and aluminum in various departments, however, when it comes to absorbing impact, sheets simply made from carbon fiber need to be avoided. Thus, making it fragile and prone to cracking and breaking down into smaller fragments. However, considering this, designers and manufacturers now combine carbon fiber composites with an aluminum honeycomb core to increase the strength and impact resistivity. Energy absorption is measured by Specific Energy Absorption (SEA). Due to this autoclave method of producing carbon fiber, this material provides the best SEA of around 40 to 60 kJ/kg as opposed to steel 12 kJ/kg and aluminum 20 kJ/kg. Thus, showing a remarkable improvement due to this improved technology.
Inflammability
One of the drawbacks of carbon fiber composites (precisely – epoxy resins) is that it is flammable and ignites when it comes into contact with fire. On the contrary, steel and aluminum sheets are more stable and provide resistance against heat. So, abstain from using carbon fiber; if you need it in a highly inflammable area as there are better options available.
All in all, carbon fiber sheets hold an advantage over traditional metals like aluminum steel in terms of the best weight to strength ratio, lightweight, minimal thermal expansion. All these properties mean that carbon fiber composites can be used in diverse industries, from automated enterprises to drones and Formula One cars. However, on the flip, one needs to take into account the high manufacturing cost associated with it when making a decision.