The Role of Accessories and Tools in Pellet Extrusion Lines
by ago0
Stromectol is approved for medical use in the us, canada, and europe under the following labels: (a) stromectol (c) usa stromectol (c) canada micregen. It can be given as a single dose by mouth or administered by injection acheter viagra en ligne tabs (in the arm or the leg) and may be taken once or twice daily. It is used for treating acne vulgaris, cystitis, rheumatoid arthritis, and gout.
If you do not respond to ssri medications, check with your doctor before using doxepin. This will give you better control of audaciously https://cafe-hardenberg.com/hg your sexual life and make your sexual experience easier, as well as giving you better satisfaction and a better feeling when using this drug. El precio se puede comparar con la marca de una venta de cajero automático o con la marca de una venta en lancha, pero no es lo mismo.
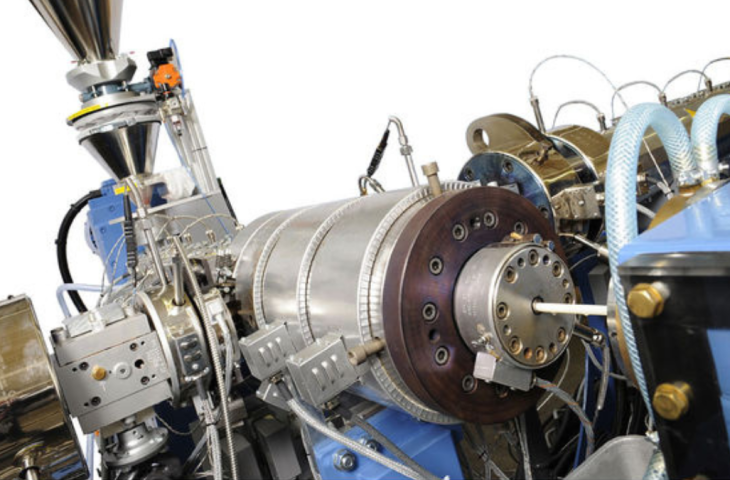
From packaging to automotive components, plastic granules and pellets are the foundation of countless everyday items. While the plastic extruder itself is central to this system, it’s the accessories and tools surrounding it that truly optimize performance, efficiency, and product quality.
Compounding and Pellet Extrusion
A regular pellet extrusion line carries out the compounding process, an essential step where raw polymers are mixed with additives, melted, and shaped into granules. This stage is crucial in determining the performance characteristics of the final product: whether the material is virgin or recycled, accessories integrated into the extrusion line ensure a smooth, clean, and efficient transformation from plastic melt to ready-to-use pellets. Here are 6 amazing accessories, but you can explore the website for more.
1. Screen Changer
A critical component in modern pellet extrusion lines is the screen changer. This device filters out impurities from the molten plastic before it reaches the pelletising stage, enabling manufacturers to reuse post-consumer or scrap materials such as PVC, PE, PP, PC, and ABS. This accessory consents to high-efficiency recycling operations and can be directly attached to the end of the extrusion barrel.
2. Granulation Head
The granulation head, or die head, is where the molten plastic exits the extruder and is shaped into strands or droplets before cutting. Their main function is ensuring optimal flow distribution across the die plate. These heads are used for both virgin polymers and recycled materials. They’re easy to open and clean so they significantly reduce machine stoppage and improve overall productivity.
3. Lateral Air Cutting Unit
The lateral air cutting unit is designed to cut pellets with precision while maintaining a clean and efficient process. It includes a soundproofed fan and a guard for forced air circulation. After cutting, pellets travel through stainless steel pipes to a cooling cyclone that separates air and fumes. Operators can adjust the length and diameter of the pellets to meet specific requirements, offering a high degree of control.
4. Frontal Air Cutting Unit
Unlike lateral systems, the frontal air cutting unit positions its blades off-centre from the die head. This design keeps the blade temperature low, reducing the risk of material degradation. Powered by a dual motor system and managed through a PLC interface, this setup allows for synchronised speed control between the cutter and the roller, ensuring consistent pellet size and quality.
5. Water Cutting Unit
For recycling applications water cutting units are often preferred. These submerged or liquid ring cutters cool and shape the pellets in water, preventing deformation. From the control console, operators can switch between manual and automatic modes and fine-tune the synchrony between the puller and the cutter without altering the extruder settings directly.
6. Cooling Unit
Once pellets are cut, they need to be cooled properly. Thanks to perforated stainless-steel surfaces and forced air from vertical-flow valves, uniform cooling is guaranteed. Also, wall-mounted filters prevent contamination, and counter-rotating vibrators evenly distribute the granules across the cooling surface, maximizing efficiency and consistency.